Basic Info.
Model NO.
HDPE-0175
Surface
Smooth
Application
Transportation Project, Hydraulic Project, Geotechnical Project, Environmental Project
Feature
Puncture Resistance, Impact Resistance, Tear Resistance
Material
HDPE
Color
Black
Transport Package
Customization
Specification
Customization
Trademark
OEM
Origin
China
HS Code
3920109090
Production Capacity
55 T/Day
Packaging & Delivery
Package Size
8000.00cm * 20.00cm * 20.00cm
Package Gross Weight
110.000kg
Product Description
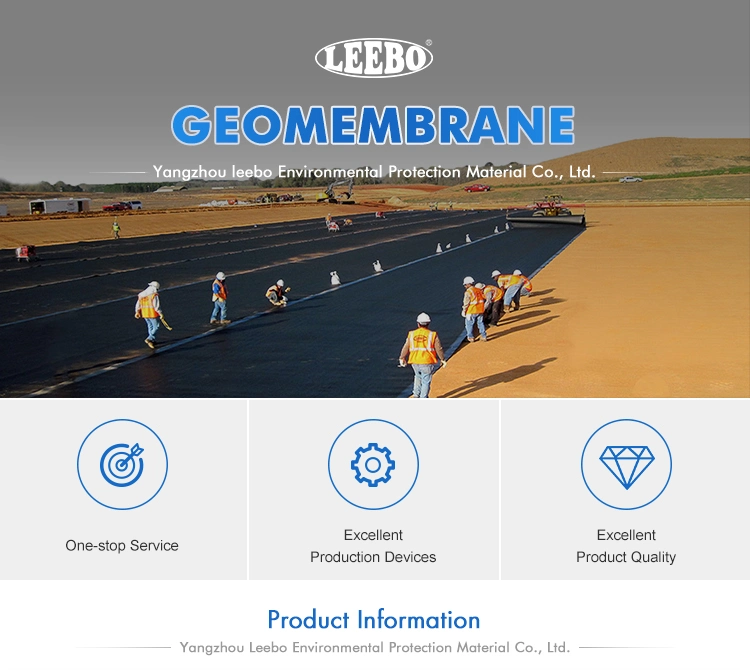
Product performance | 1. High anti-seepage coefficient 2. Chemical stability 3. Anti-aging performance 4. Good economic benefits 5. Construction speed is fast 6. Environmentally friendly and non-toxic |
Application field | 1. Environmental protection 2. Water conservancy 3. Aquaculture industry 4. Garden 5. Chemical plant, refinery 6. Mining 7. Transportation facilities 8. Agriculture 9. Subway, planting roof, sewage pipe 10. Salt film, salt pool crystallization pool |
Glossy geomembrane introduction | Glossy HDPE geomembrane is a geomembrane product with a smooth surface on both sides. It is made of high quality high density polyethylene material, which is made of a combination of about 97.5% polyethylene, 2.5% carbon black, a trace amount of antioxidant and heat stabilizer. The resin used in the production process is specially designed for geomembrane. Applied raw polyethylene resin raw materials |
Rough geomembrane introduction | The single-faced HDPE geomembrane is a geomembrane product that forms a matte surface by nitrogen pressure jetting on the basis of a glossy geomembrane. This process is the only way to produce a matte geomembrane without significantly reducing any of its physical properties. The geomembrane product is made of high quality high density polyethylene material, which is made of a combination of about 97.5% polyethylene, 2.5% carbon black, a trace amount of antioxidant and heat stabilizer. The resin used in the production process is designed for The raw polyethylene resin raw material actually prepared by the geomembrane application. |
No. | index | test value | ||||||
0.75mm | 1.00mm | 1.25mm | 1.50mm | 2.00mm | 2.50mm | 3.00mm | ||
1 | Minimum density(g/cm²) | 0.93 | ||||||
2 | Yield Strength,N/min | 11 | 15 | 18 | 22 | 29 | 37 | 44 |
Breaking strength,N/min | 20 | 27 | 33 | 40 | 53 | 67 | 80 | |
Yield elongation ratio | 12 | |||||||
Breaking elongation ratio | 700 | |||||||
3 | Right angle tear strength,N | 93 | 125 | 156 | 187 | 249 | 311 | 374 |
4 | Piercing strength,N | 240 | 320 | 400 | 480 | 640 | 800 | 960 |
5 | Resistant to environmental stress cracking,hr | 300 | ||||||
6 | Carbon black | |||||||
Carbon black content,% | 2.0-3.0 | |||||||
Carbon black dispersion | Nine of the ten observation areas should belong to Stage 1 or Stage 2, and Stage 3 should not be more than one. | |||||||
7 | Oxidation induction time | |||||||
Standard OIT,(min) | 100 | |||||||
High pressure OIT,(min) | 400 | |||||||
8 | 85 baking aging(Min average) | |||||||
After baking 90d,Standard OIT % | 55 | |||||||
Baking 90d,High pressure OIT % | 80 | |||||||
9 | UV resistance | |||||||
Ultraviolet radiation 1600h, Standard OIT % | 50 | |||||||
Ultraviolet radiation 1600h, High pressure OIT % | 50 | |||||||
10 | -70 Low temperature shock enchantment performance | Pass through | ||||||
11 | Water vapor permeability coefficient | ≤1.0*10-13 | ||||||
12 | Dimensional stability | ±2 |
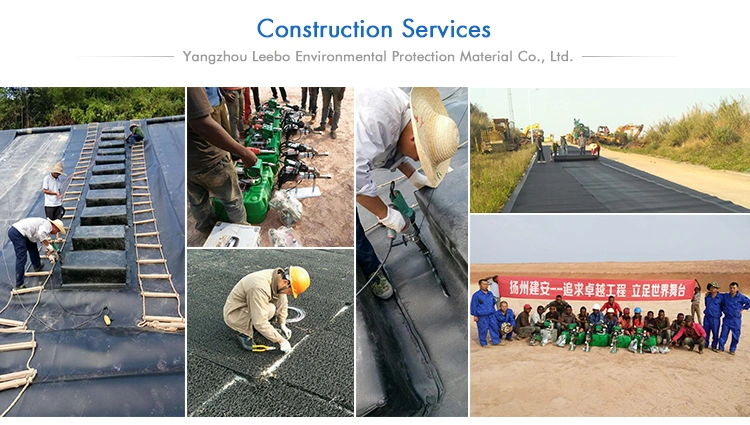
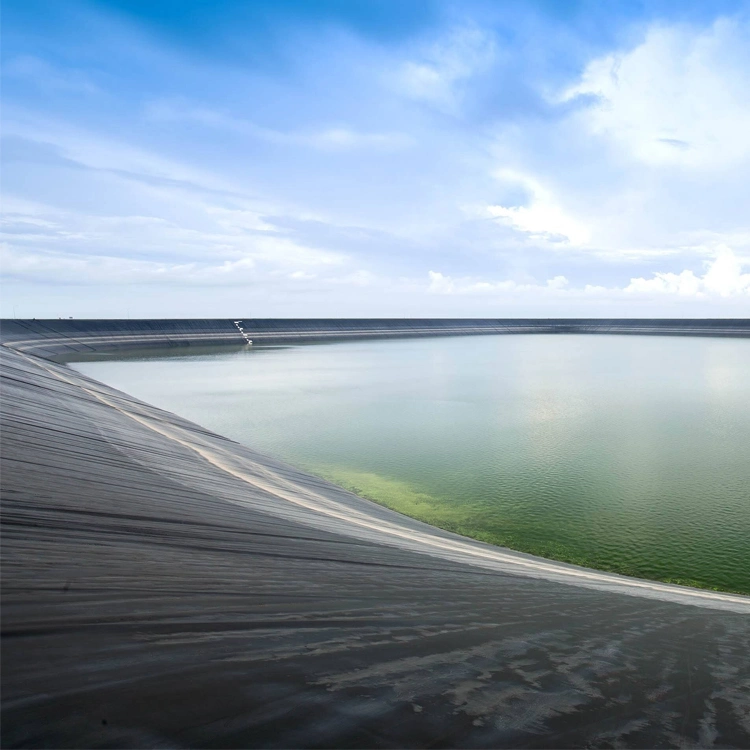

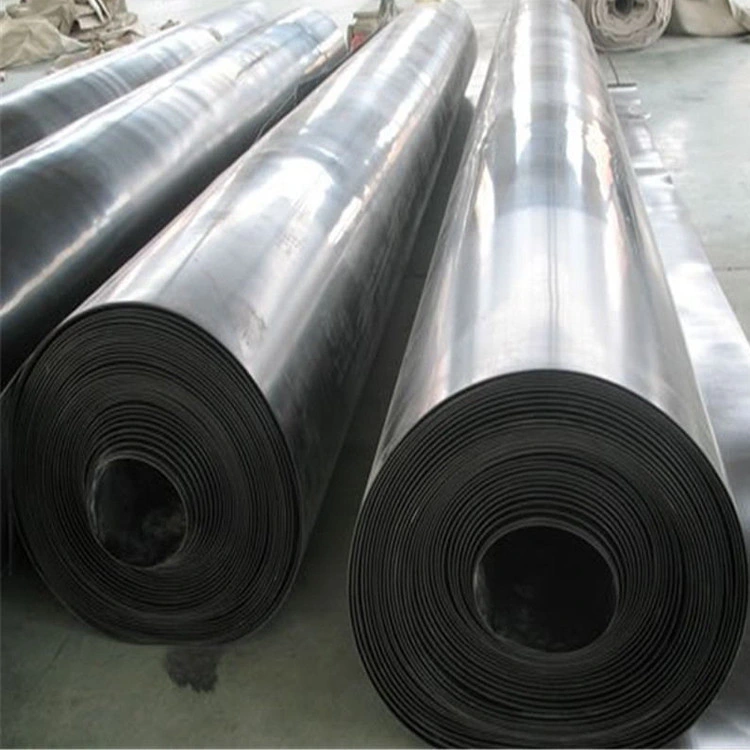
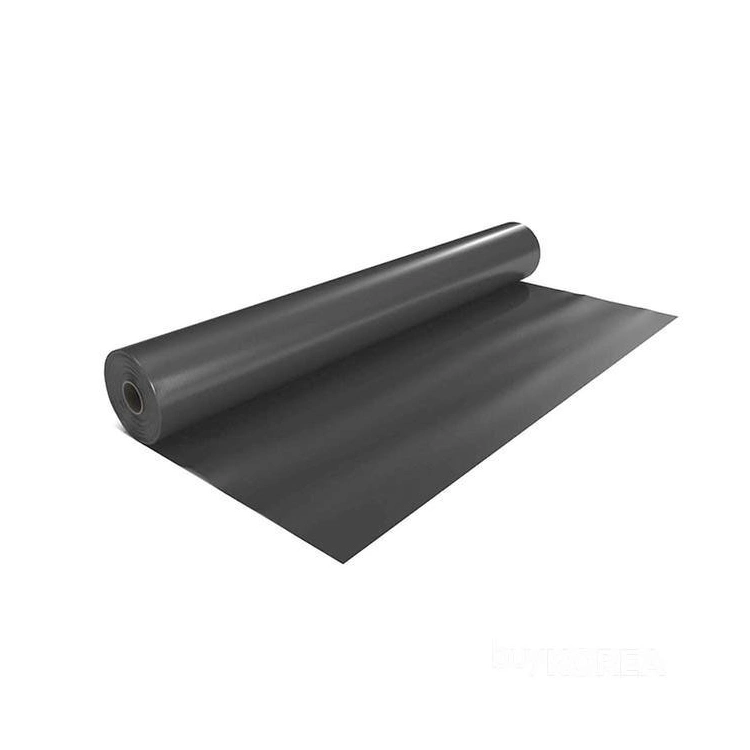
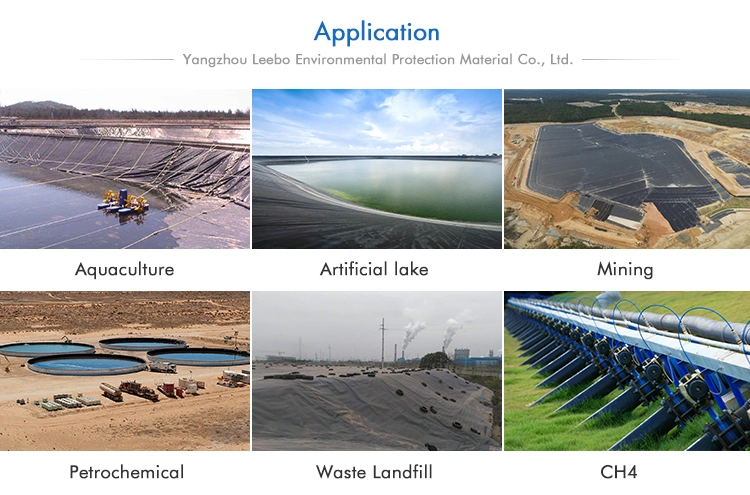
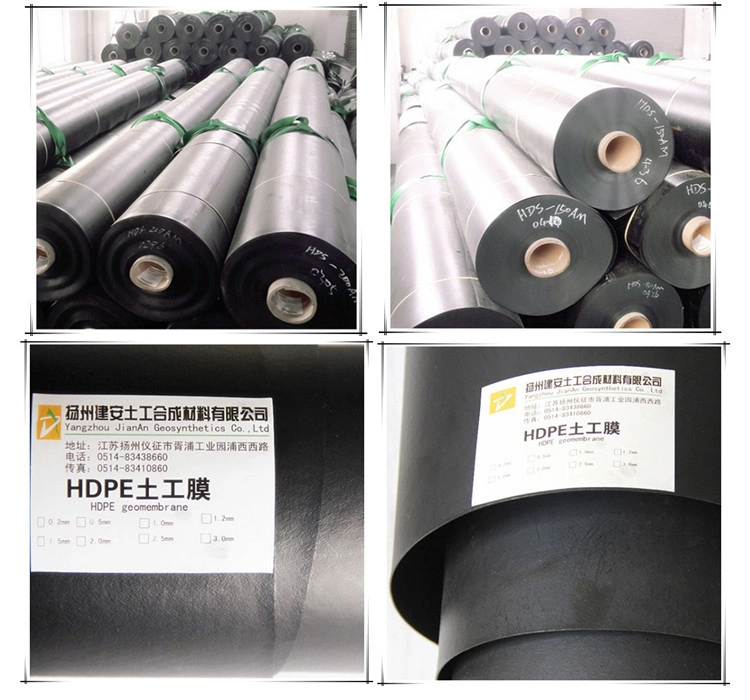
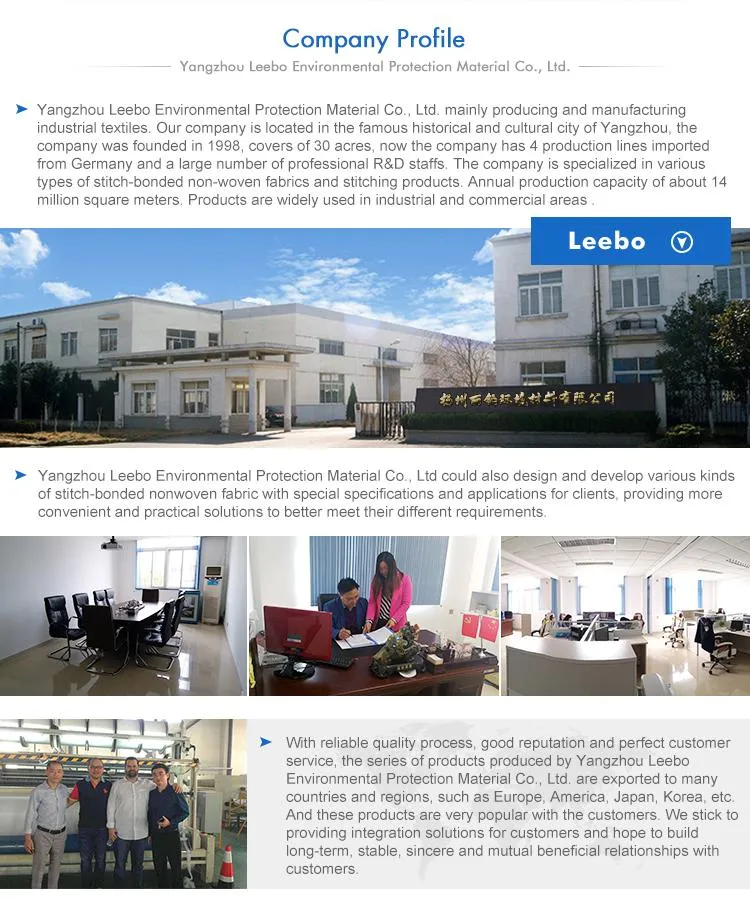
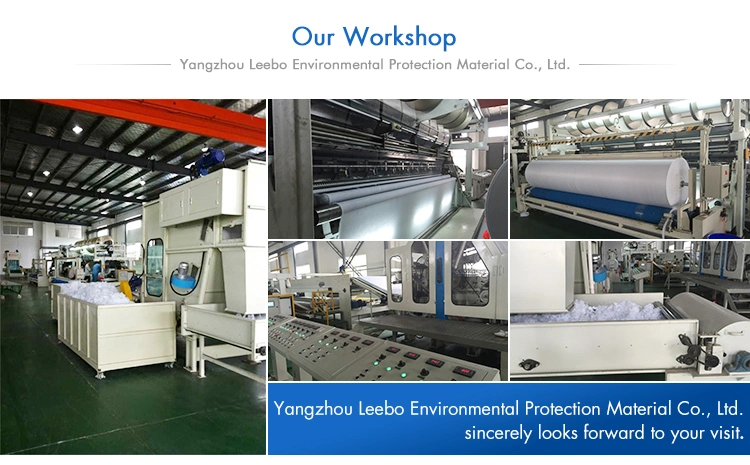